Manufacturing Intelligence
Welcome to The Manufacturing Intelligence Show—where innovation meets manufacturing. Join hosts Andrew Scheuermann, Co-founder and CEO, and Jennifer Davis, VP of Communications & Marketing at Arch Systems, as they dive into the latest trends in AI, digitization, and advanced technologies. Discover how these innovations are reshaping the industry and unlocking new opportunities for growth and efficiency. Tune in for expert insights, thought-provoking conversations, and practical strategies to stay ahead in the evolving world of manufacturing.
Episodes
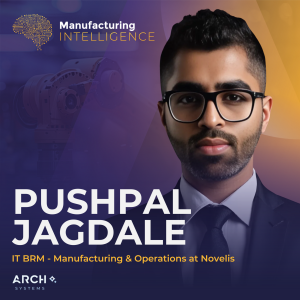
Friday Jun 27, 2025
Friday Jun 27, 2025
Novelis's IT BRM of Manufacturing & Operations Pushpal Jagdale’s approach to manufacturing transformation challenges the technology-first mentality that derails most digitization efforts. His experience scaling connected systems across hundreds of machines at Honeywell, then transitioning to safety-critical AI applications at Novelis, illustrates why business alignment trumps technical sophistication in successful deployments.
Pushpal shares his methodology for cataloguing legacy assets before attempting any connectivity projects, explaining how understanding which machines can actually integrate with enterprise networks prevents expensive pilot failures. The conversation with Jennifer and Andrew also explores how safety-focused AI applications create the strongest business cases in heavy manufacturing environments.
Topics discussed:
Asset cataloguing methodologies for legacy system integration before attempting digital transformation initiatives across global manufacturing operations.
The strategic approach to AI business case development that starts with personal productivity applications like meeting transcription before advancing to factory-specific implementations.
Safety-first AI deployment strategies using autonomous inspection robots in hazardous environments to eliminate operator exposure risks.
Global scaling frameworks for digital transformation that account for non-standardized assets, processes, and product portfolios across international facilities.
IT-OT alignment strategies that transform traditional client-vendor relationships into true partnerships through shared vision and collaborative execution models.
Data strategy fundamentals as the foundation for successful AI deployment, including quality requirements and contextualization of legacy equipment outputs.
Predictive maintenance applications using sensor-mounted machine learning models that integrate vibration, temperature, and torque data with product and process information.
The evolution from discrete electronics manufacturing to metals processing and how core operational objectives remain consistent across different manufacturing environments.
Knowledge management AI systems that convert SOPs and training materials into searchable troubleshooting resources for new engineers working with legacy equipment.
Listen to more episodes:
Apple
Spotify
YouTube
Website
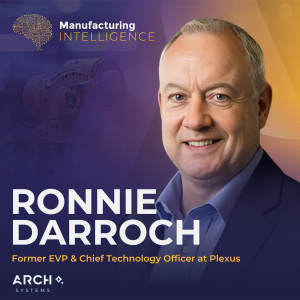
Monday Jun 23, 2025
Monday Jun 23, 2025
The most honest assessment of manufacturing leadership comes from someone who's lived through four decades of industry transformation — and our guest in this episode of Manufacturing Intelligence. Ronnie Darroch, former EVP and CTO at Plexus, doesn't sugarcoat the reality: technology is the easy part, getting people to act on insights is where most digital transformations fail.
Ronnie's career from component-level PCB repair to global executive reveals a consistent pattern: discretionary effort, not technology, determines competitive outcomes. His contrarian 80/20 rule advocates spending 80% of effort on culture and management processes, only 20% on connectivity. The conversation explores his systematic approach to global collaboration, AI governance frameworks, and why customer trust architecture matters more than contracts in low-margin manufacturing.
Topics discussed:
The discretionary effort framework for competitive advantage, explaining why voluntary team performance differentiates companies and how leaders create conditions to inspire it through authentic relationship-building rather than traditional management.
The 80/20 smart manufacturing rule prioritizing culture over connectivity, demonstrating why "getting data is the easy part" while building management processes to act on insights requires systematic cultural transformation.
Metrics management Hippocratic oath introducing the "do no harm" principle, including real examples of misaligned incentives destroying production flow and the diagnostic question: "Is your metrics system making you more competitive?"
Global collaboration systematic approach for multi-regional leadership, covering strategic face-to-face kickoff investments, rotating governance schedules, and leveraging diversity to achieve "1+1=3" team performance across cultures.
AI governance without stifling innovation, addressing artificial intelligence's trust problem through human accountability frameworks while leveraging technology for productivity gains, referencing "The Atomic Human" for manufacturing leaders.
Customer trust architecture mechanics in contract manufacturing's 10% margin environment, breaking down how every interaction builds or erodes relationships and why collaborative problem-solving outperforms contractual enforcement.
Early career acceleration principles from promotion to department manager at 24, emphasizing how "someone must give you a chance to lead" and why hands-on work understanding creates lasting team credibility.
Single-piece flow intuition development from PCB debugging experience, illustrating how cellular manufacturing with immediate feedback can emerge naturally when questioning established batch processes.
Listen to more episodes:
Apple
Spotify
YouTube
Website
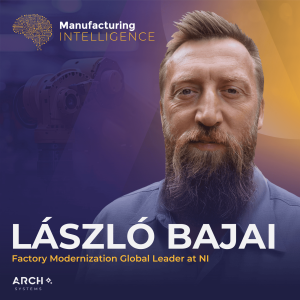
Thursday Jun 05, 2025
Thursday Jun 05, 2025
The most honest assessment of factory modernization you'll hear comes from someone who's lived through decades of digital transformation failures and successes — and our guest in this episode of Manufacturing Intelligence. László Bajai, Factory Modernization Global Leader at National Instruments, doesn't sugarcoat the reality: companies claiming to be "super digital" often still use paper to assemble AI-driven products.
László's early realization that he wanted to improve engineering processes rather than just implement solutions set the foundation for a career focused on domain understanding first, automation second. This perspective shapes his approach to every modernization project, where he consistently prioritizes people, then process, then technology. The conversation also explores his three non-negotiable pillars for factory modernization: brutal honesty about current maturity levels, comprehensive human engagement across all organizational levels, and flexible openness to external solutions.
Topics discussed:
The importance of multidisciplinary expertise in manufacturing modernization, combining domain knowledge with technical skills rather than pure implementation focus to drive meaningful process improvements.
Why Plan B and Plan C thinking becomes essential for project success, illustrated through real examples of last-minute personnel changes and how preparation for multiple scenarios ensures delivery even when primary strategies fail.
Human-centered change management strategies that address resistance from engineering teams, including techniques for buying in stakeholders, involving them in testing phases, and managing expectations across cultural and geographical boundaries.
Model-based enterprise frameworks that eliminate traditional 2D drawing workflows, replacing annotation-heavy processes with data-driven approaches that enable end-to-end traceability from customer requirements through manufacturing and quality.
Smart scale integration methodologies for inventory precision improvement, demonstrating how MES systems connect real-time material consumption data to ERP systems while revealing underlying process problems that digitization exposes rather than solves.
Three pillars of successful factory modernization: maturity assessment honesty, comprehensive human engagement, and flexible openness to external solutions, emphasizing why technology selection becomes the smallest challenge when foundational elements are properly addressed.
Global stakeholder management tactics requiring embedded local champions, ensuring project knowledge and decision-making authority exists at every geographic location rather than centralizing expertise at headquarters.
Enterprise-level AI vision for competitive advantage creation, connecting machine-level OT data through ERP and SharePoint systems to enable organization-wide intelligent query capabilities that transform data accessibility and decision-making speed.
Why technology must prove itself innocent rather than being assumed guilty, addressing the natural human tendency to blame new systems first and strategies for building trust through transparent data quality and systematic problem-solving approaches.
Listen to more episodes:
Apple
Spotify
YouTube
Website
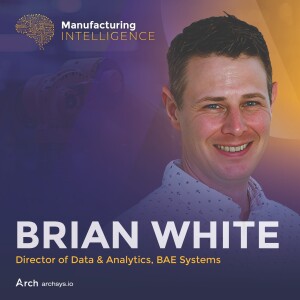
Thursday Jan 30, 2025
Thursday Jan 30, 2025
Brian White, Director of Data & Analytics at BAE Systems, embodies the evolving face of modern manufacturing leadership. Manufacturing operations in highly regulated industries face unique challenges, such as balancing innovation with strict security requirements, connecting disparate data systems, and maintaining the highest quality standards. Brian and his team at BAE Systems are tackling these challenges head-on by implementing sophisticated data analytics solutions that work "from the Factory Floor to the Boardroom."
In this episode of Manufacturing Intelligence, Brian joins Jennifer and Andrew shares his vision for digital twins, connected production lines, and AI-powered flexible scheduling. He discusses practical approaches to implementing these technologies in highly regulated environments, building trust with operators and leadership, and the critical importance of data literacy in driving transformation.
Topics discussed:
Building scalable data analytics solutions that connect factory floor operations to boardroom decision-making in regulated environments.
Implementing generative AI and advanced analytics while maintaining compliance with DFARS and CMMC requirements in defense manufacturing.
Creating digital thread capabilities that connect design, production, and field data to enhance manufacturing operations and product quality.
Empowering operators through digital twins and connected systems to improve first-time quality and reduce production issues.
Developing trust-based leadership approaches to drive adoption of new technologies and data-driven methodologies across the organization.
Building global solutions that can scale across multiple facilities while reducing maintenance overhead and technical debt.
Balancing innovation and security requirements in aerospace and defense manufacturing environments.
Leveraging AI and automation to create more flexible, efficient production lines that can adapt to changing demands.
Fostering data literacy and education to enable effective use of analytics tools and insights across the organization.
Listen to more episodes:
Apple
Spotify
YouTube
Website
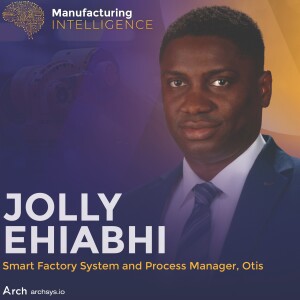
Thursday Jan 16, 2025
Thursday Jan 16, 2025
In this episode of Manufacturing Intelligence, Jennifer, and Andrew sit down with Jolly Ehiabhi, Smart Factory System and Process Manager, at Otis, who shares his remarkable journey from agricultural engineering in Lagos to spearheading Industry 4.0 initiatives. Jolly's unique approach combines deep technical expertise with a strong focus on people and team building, making him a standout leader in manufacturing transformation.
He offers valuable insights on implementing real-time monitoring solutions, navigating legacy system integration, and building effective cross-functional teams. The conversation also explores practical strategies for digital transformation success, Jolly’s predictions for the future of AI in manufacturing, and the exciting potential of predictive maintenance and digital twins.
Topics discussed:
Implementing successful real-time monitoring solutions through careful stakeholder engagement and cross-functional team building strategies.
Integrating legacy systems and new technologies, including practical approaches to machine connectivity and data collection.
The role of predictive maintenance in reducing costly downtime and improving manufacturing efficiency through data-driven insights.
Developing and implementing digital twin technology for improved factory visualization and operational planning.
The importance of balancing technical innovation with people-first leadership approaches in manufacturing transformation.
Practical implementation of Industry 4.0 initiatives, including shop floor visualization and real-time monitoring systems.
The evolution of manufacturing analytics from spreadsheets to advanced visualization tools and predictive capabilities.
Future opportunities in manufacturing intelligence, including AI implementation and the potential for increased operational efficiency.
Listen to more episodes:
Apple
Spotify
YouTube
Website
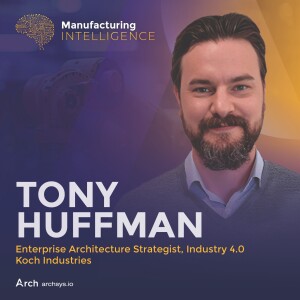
Friday Dec 20, 2024
Friday Dec 20, 2024
In this episode of Manufacturing Intelligence, Jennifer and Andrew chat with Tony Huffman, Enterprise Architecture Strategist, Industry 4.0 at Koch Industries. Tony emphasizes the critical need for a unified namespace to ensure data consistency across systems, which is essential for effective decision-making.
He also discusses the importance of balancing operational excellence with technological advancements, highlighting how organizations can leverage AI to enhance workforce capabilities. Additionally, he addresses the significance of a people-first approach to change management, advocating for continuous learning and engagement to drive successful transformation efforts.
Topics discussed:
The critical role of a unified namespace in ensuring data consistency across manufacturing systems for effective decision-making and analytics.
Balancing operational excellence with technological advancements to achieve sustainable growth in manufacturing environments.
The importance of a people-first approach to change management in driving successful digital transformation initiatives.
Leveraging AI to augment workforce capabilities and enhance efficiency on the shop floor.
The limitations of traditional ROI metrics in measuring the value of digital transformation efforts in manufacturing.
Strategies for fostering a culture of continuous learning and adaptation within organizations to keep pace with industry changes.
Capturing tacit knowledge and integrating it with structured data for better insights and decision-making.
The impact of regulatory environments on innovation and transformation in heavily regulated industries like medical devices and aerospace.
Best practices for implementing lean daily management practices to stabilize operations before introducing new technologies.
The evolving role of leadership in guiding teams through digital transformation and ensuring alignment with organizational goals.
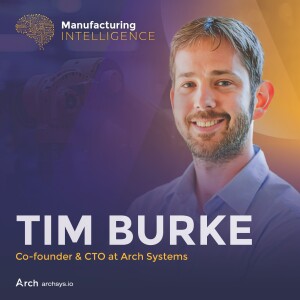
Wednesday Dec 04, 2024
Wednesday Dec 04, 2024
In this episode of Manufacturing Intelligence, Jennifer and Andrew welcome a familiar face as their guest expert — Tim Burke, co-founder and CTO of Arch Systems. Tim shares his insights on the transformative role of artificial intelligence in electronics manufacturing, discussing the challenges and opportunities of integrating AI technologies into existing processes.
Tim also emphasizes the importance of data standardization and collaboration across teams. He highlights how AI can streamline operations, enhance product quality, and reduce costs, ultimately driving innovation in the industry. Additionally, Tim addresses the need for capturing tacit knowledge to empower the next generation of engineers.
Topics discussed:
The increasing complexity of electronic components and how it impacts manufacturing processes, requiring innovative solutions to maintain efficiency and quality.
The talent gap in the manufacturing workforce and the need for training and mentorship to prepare the next generation of engineers.
The significance of data integration and standardization in overcoming the data dilemma faced by many electronics manufacturers today.
Strategies for capturing tacit knowledge from experienced workers to ensure valuable insights are preserved and shared within the organization.
The role of AI in automating data management processes, and how it allows manufacturers to make informed decisions based on real-time insights.
The importance of fostering a culture of collaboration and continuous learning to fully leverage AI technologies in manufacturing environments.
How AI can enhance product quality and reduce costs by streamlining operations and minimizing errors in the manufacturing process.
The potential for AI-driven analytics to predict equipment failures and optimize maintenance schedules, improving overall operational efficiency.
The future of manufacturing with AI, focusing on creating a virtual layer that connects all machines and processes for better visibility.
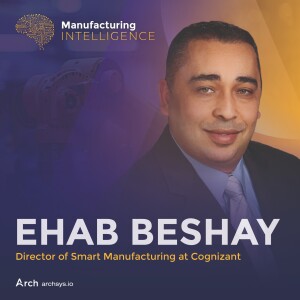
Tuesday Oct 15, 2024
Tuesday Oct 15, 2024
In a recent episode of the Manufacturing Intelligence show, Ehab Beshay, Director of Smart Manufacturing at Cognizant, shares his expertise on digital transformation and automation within the manufacturing sector. He discusses the importance of cultural adaptation when leading complex engineering projects, emphasizing how understanding diverse communication styles can enhance collaboration.
Ehab also dives into the role of artificial intelligence in optimizing manufacturing processes, highlighting its potential to improve decision-making and operational efficiency. With over 20 years of experience, Ehab provides valuable insights into the challenges and opportunities that come with integrating new technologies in a rapidly evolving industry.
Topics discussed:
The significance of digital transformation in manufacturing and how it can lead to improved efficiency and productivity.
The need for engineers to adapt their communication styles to different cultures when managing international projects for better collaboration.
How artificial intelligence can enhance decision-making processes and operational efficiency within manufacturing environments, driving innovation and competitiveness.
The importance of involving all stakeholders in the transformation process is highlighted, fostering a sense of ownership and ensuring project success.
Effective communication strategies that encourage team members to share ideas and opinions, which is crucial for fostering innovation.
The latest automation technologies and their impact on manufacturing processes, including benefits and potential pitfalls.
How data can be leveraged for optimization and utilization, driving better outcomes in manufacturing operations.
The need for workforce upskilling to keep pace with technological advancements and ensure employees are equipped for future challenges.
The importance of having a clear vision for digital transformation, ensuring that organizations focus on meaningful solutions rather than just tools.
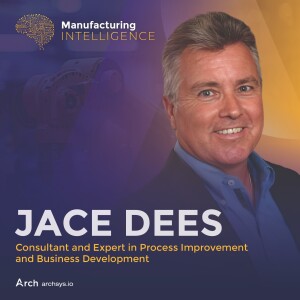
Tuesday Oct 15, 2024
Tuesday Oct 15, 2024
In this episode of Manufacturing Intelligence, Jennifer and Andrew catch up with Jace Dees, a Consultant and Expert in Process Improvement and Business Development. Jace taps into his extensive experience in electronics manufacturing to highlight the transformative impact of strategic innovation and artificial intelligence on the industry. He discusses the critical role of AI in enhancing operational efficiency and decision-making processes, emphasizing how data-driven insights can lead to significant improvements.
Jace also addresses the challenges of transitioning from high-volume to low-volume, high-mix production, and the importance of effective communication during such changes. With over 25 years in the field, Jace provides valuable perspectives on navigating the complexities of global operations and the future of manufacturing.
Topics discussed:
The transformative role of artificial intelligence in enhancing operational efficiency and decision-making processes within the electronics manufacturing industry.
Strategies for navigating the challenges of transitioning from high-volume to low-volume, high-mix production environments in manufacturing settings.
The importance of effective communication and over-communication during transitions to ensure alignment and clarity among team members and stakeholders.
Leveraging data-driven insights to identify trends and optimize processes, ultimately driving innovation and operational excellence in manufacturing.
The significance of talent development and maintaining a focus on lean six sigma principles to foster continuous improvement.
Exploring the integration of advanced technologies and automation to address labor challenges and improve supply chain resilience.
The impact of global operations on supply chain management and the need for diversification to minimize risks.
Insights into the future of manufacturing, including the evolving role of AI and digitization in shaping industry practices.
The necessity of understanding customer perceptions and managing relationships across various business units to drive success.
Strategies for fostering collaboration among cross-functional teams to achieve operational goals and enhance overall performance.
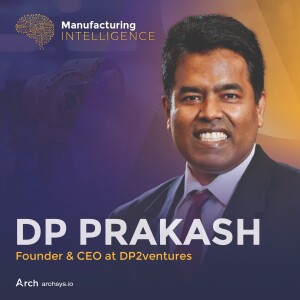
Tuesday Oct 15, 2024
Tuesday Oct 15, 2024
In our inaugural episode of the Manufacturing Intelligence show, hosts Andrew Scheuermann, Co-founder & CEO, and Jennifer Davis, VP of Communications & Marketing at Arch Systems, welcome their first guest, DP Prakash, Founder & CEO of DP2ventures, who shares his extensive experience in semiconductor manufacturing and the pivotal role of mentorship in driving innovation. He discusses how guidance from influential mentors has shaped his career and fostered a culture of creativity and risk-taking in technology.
DP also explores the integration of AI and augmented reality in training, highlighting how these technologies can revolutionize skill development and enhance operational efficiency. Listeners will gain valuable insights into the future of the tech industry and learn how collaboration and mentorship can unlock potential and inspire the next generation of leaders.
Topics discussed:
The transformative impact of mentorship on personal and professional growth in the technology sector, particularly the importance of guidance from experienced leaders.
How collaboration fosters innovation, encouraging open dialogue among teams to navigate challenges and seize opportunities in semiconductor manufacturing.
The integration of AI and AR in training programs, and how these technologies can improve learning efficiency and operational effectiveness.
The role of innovation labs in advancing technology and how they serve as incubators for new ideas and solutions across various regions.
Strategies for reducing training times and improving factory efficiency through innovative technologies, ultimately leading to enhanced productivity in manufacturing processes.
The importance of understanding business use cases when implementing new technologies, ensuring that innovations align with organizational goals and competitive advantage.
Insights into the future of semiconductor manufacturing, discussing emerging trends and the need for adaptability in a rapidly evolving technological landscape.
The significance of creating a culture of creativity and risk-taking within organizations to drive continuous improvement and breakthrough innovations.